Just In Time (JIT) is a popular inventory management strategy that aims to streamline production processes by minimizing inventory levels and bringing materials or products to the production line exactly when they are needed. This method was first introduced by Toyota in the 1970s and has since been adopted by many industries worldwide.
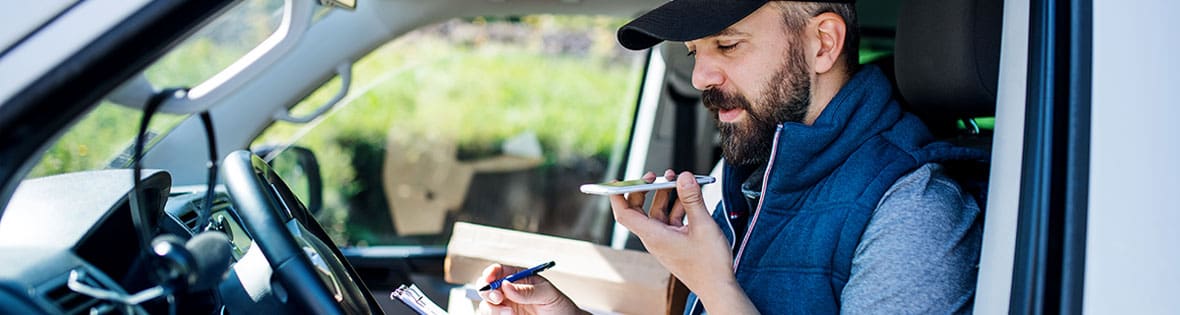
Credit: www.netsuite.com
Table of Contents
How does the Just In Time method work?
The Just In Time method focuses on reducing waste, improving efficiency, and increasing productivity. It involves close coordination with suppliers, as materials are only delivered when they are needed for production. By minimizing inventory levels, companies can free up capital that would otherwise be tied up in inventory costs.
The JIT method relies on accurate demand forecasting and a well-coordinated supply chain. It requires suppliers to have the ability to deliver materials quickly and in small quantities. This enables companies to respond rapidly to changes in customer demand, reduce storage costs, and eliminate the risk of holding obsolete or slow-moving inventory.
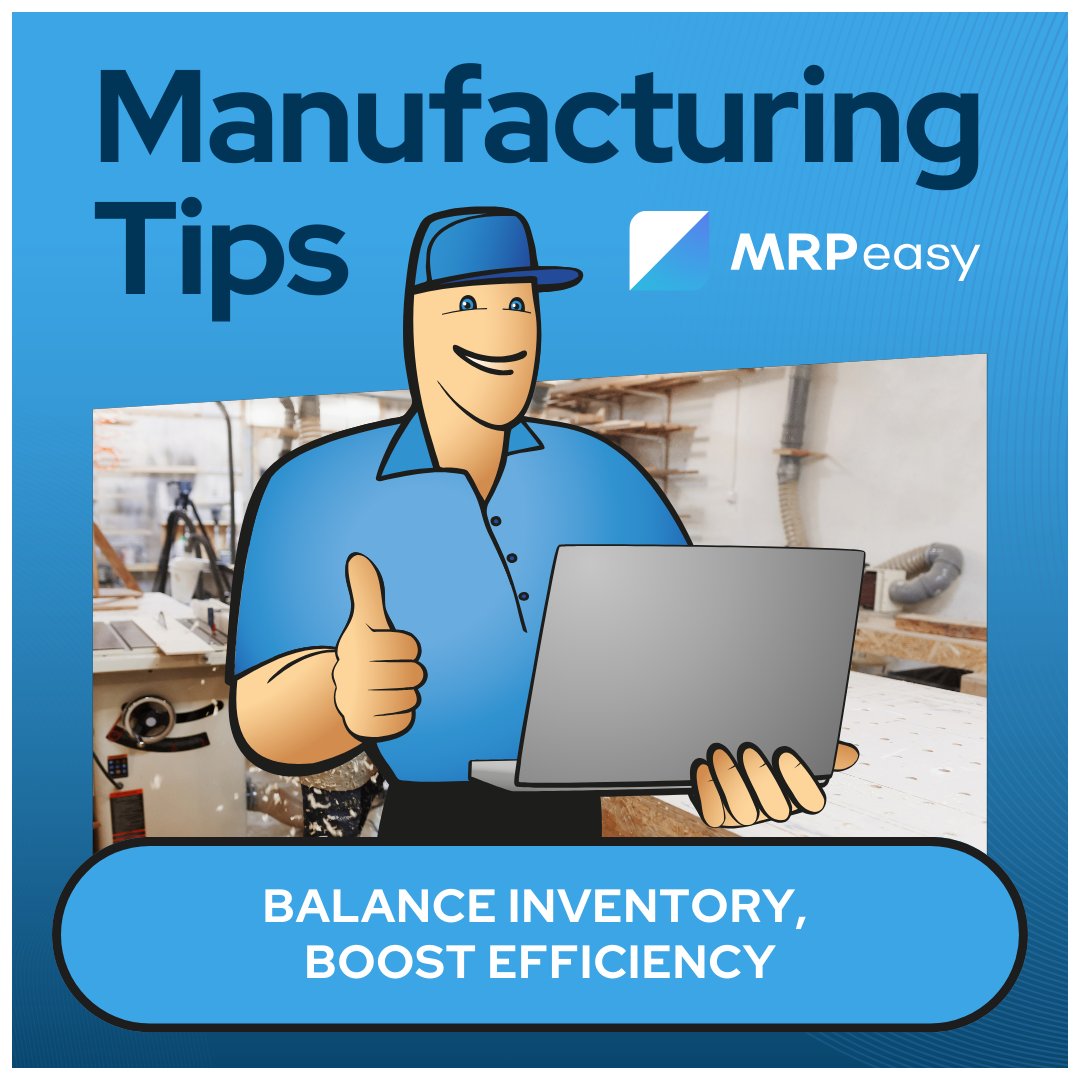
Credit: twitter.com
Benefits of the Just In Time method
The Just In Time method offers several benefits to companies who implement it effectively:
- Reduced Inventory Costs: By keeping inventory levels low and eliminating the need for excessive storage space, companies can significantly reduce inventory carrying costs.
- Improved Cash Flow: With less capital tied up in inventory, companies can allocate their resources to other areas of their business, improving cash flow and financial stability.
- Reduced Waste: JIT helps to minimize waste by avoiding overproduction, excess inventory, and unnecessary movement of materials.
- Increased Efficiency: By delivering materials or products just in time, companies can optimize production processes and reduce lead times, ultimately increasing overall efficiency.
- Enhanced Quality: JIT emphasizes the importance of quality control at each stage of production, reducing the risk of defects and improving overall product quality.
Potential Challenges with JIT
While the Just In Time method offers numerous advantages, it is important to be aware of potential challenges that may arise when implementing this strategy:
Challenge | Solution |
---|---|
Supplier Reliability | Implement effective supplier management and establish strong relationships with reliable suppliers. |
Accuracy of Demand Forecasting | Invest in advanced forecasting methods and adopt a data-driven approach to demand planning. |
Production Interruptions | Implement contingency plans to address potential production disruptions and ensure backup suppliers are available if needed. |
Tightly Coordinated Supply Chain | Ensure effective communication and collaboration between all stakeholders in the supply chain. |
By addressing these challenges and implementing appropriate strategies, companies can overcome potential hurdles and fully leverage the benefits of the Just In Time method.
Conclusion
The Just In Time method is an effective approach to inventory management that focuses on reducing waste, improving efficiency, and increasing productivity. By minimizing inventory levels and delivering materials or products just in time, companies can significantly reduce costs, improve cash flow, and enhance overall operational performance. However, it is crucial to carefully plan, coordinate, and address potential challenges to ensure successful implementation of JIT.